Beyond the Tissue Plant – Essity’s Barton Facility on a Roll with Employee Satisfaction and Sustainability
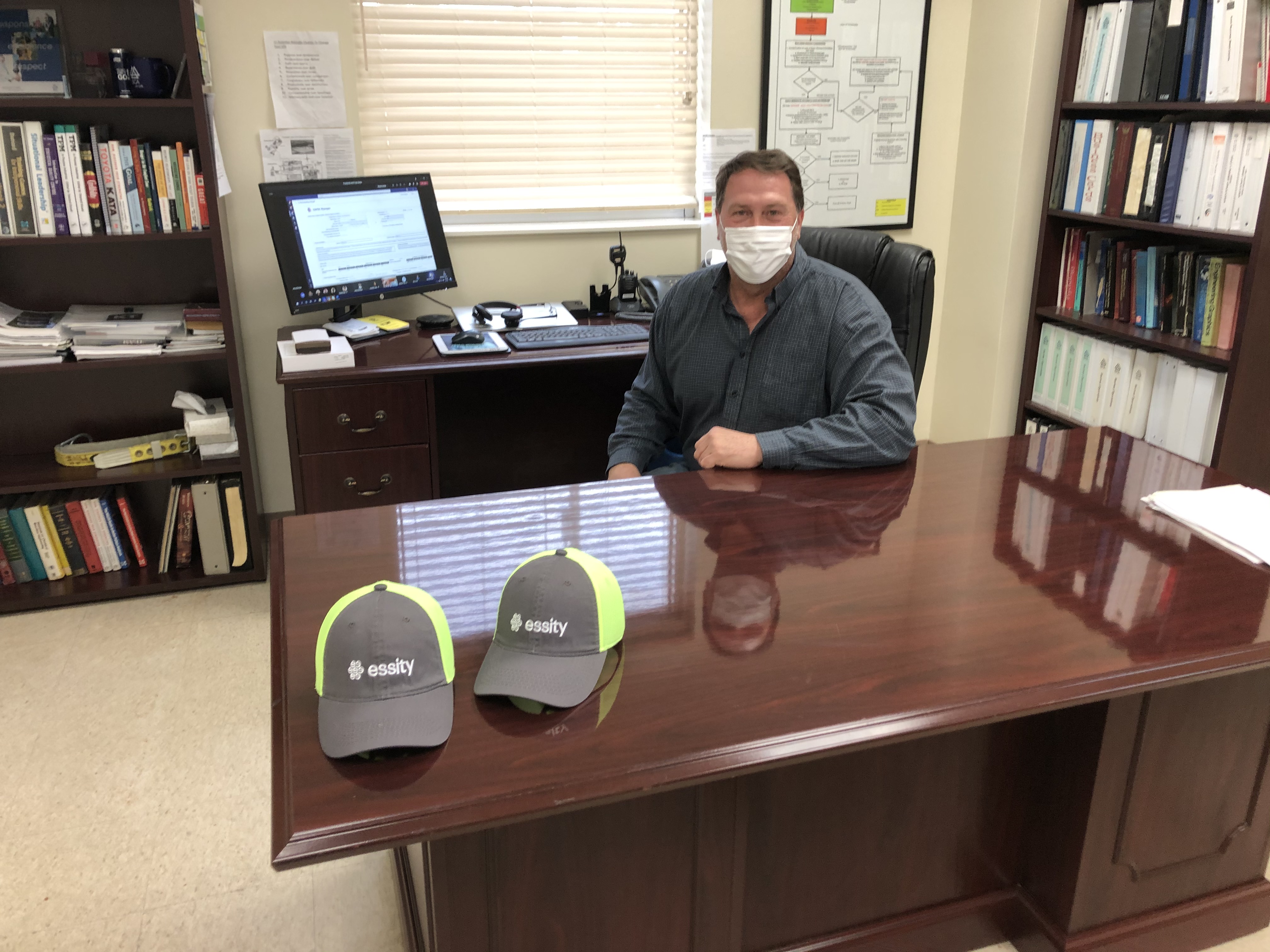
Many may refer to it as the “tissue plant” in Barton, but tissue production is only one of the things happening locally at leading hygiene and health company Essity’s plant.
Essity (previously known as ‘SCA’ until 2017) has been a member of the Cherokee community for nearly 16 years. Its 1.2-million-square-foot location in Barton employs nearly 500 Shoals area residents and makes the Tork® brand of paper products (tissues, napkins, paper towels). The facility—built in 2003 as a brand new ‘greenfield’ site—does it all: manufacturing, converting and distributing Tork products throughout the region.
You can find Tork products in many of your favorite restaurants and well-known food service businesses in the region. Tork products are also used in local schools, businesses, sports arenas and other venues.
Steve Edwards, Essity Site Manager for Barton, is passionate about the Tork paper products people use every day, but even more, he’s passionate about the people who make these products, and the surrounding community Essity serves.
“We have a fantastic crew at Barton,” said Edwards. “It is an understatement to say that 2020 was a challenging year for everyone, and as we make our way into 2021, our team continues to go above and beyond every day.”
Steve spent some time with our Chamber newsletter team to give us a look inside Essity’s walls, talking about operating during the pandemic, the company’s commitment to sustainability, and some highlights of Essity’s community involvement and internal initiatives that help to make it a great place to work.
Tell us how/why Essity remained open for business during the pandemic
As an essential products company, it is crucial for us to do everything we can to safely remain in operation and maintain our manufacturing footprint. To give you an idea of what we mean by ‘essential’ employees, of the 500 on staff here, 470 of those individuals have continued to work in person, on-site, nonstop. With COVID-19, the health and safety of our employees and their families has beenꟷ and remainsꟷ our first and primary concern. One of the initial steps Essity’s leadership took early last year, when we foresaw the significant global impact COVID-19 would have, was to partner with health agencies and specialists in the field to rapidly develop global health, safety and production standards for all manufacturing sites. Even before state and local requirements were established for masks and social distancing, our Barton team had its pandemic plan in place. Some of the protocols we immediately adopted (and are still in place today) include:
- Temperature scanning: We have an advanced walk-through machine at our entrances.
- Socially distanced work environment: We eliminated common area meeting spots; all meetings are held virtually; we brought in a dozen office trailers situated around the perimeter of our building to spread teams out even further. Those trailers will likely be in place most of this year.
- Voluntary furloughs: Over the last part of 2020, product demand temporarily declined, which meant that in the short term, we did not need full team staffing over our four-shift, 24/7 cycle. Rather than initiate layoffs, we instead offered team members the opportunity to voluntarily furlough, with a set return date and no loss of benefits. The response was overwhelmingly positive – we had more than enough volunteers, and their willingness to furlough enabled us to maintain productivity without hardship, retaining our great team, and their skillsets that are critical.
- COVID-19 Pay: To ensure that our employees felt comfortable taking time to stay at home due to potential exposure to COVID-19 (or that of their family members), and even more importantly, to give them the confidence that their jobs were secure upon their return, we offer(ed) 80 hours of pay to take off for such a reason. This was above and beyond sick pay or vacation time.
- On-site COVID Testing: To ensure that our employees have confidence coming into the workplace, we invested in offering on-site COVID testing to all employees. Our plant nurse and safety manager are both trained in administering the tests.
How have these health and safety protocols been received by your employees? I’m proud to say that our team has embraced these workplace changes, and morale at Essity is positive. This is mainly because we have been transparent with our team from the beginning of the pandemic, from implementation of safety measures, public health updates and introduction of new technologies, to staffing issues – all of it. We are also lucky to have a terrific working relationship with our local United Steel Workers (USW) union. The local USW President, Calvin (Buck) Bolden, has been an active participant in our conversations as we enacted all of the protocols listed above, and he and the USW team have been strong sounding boards as we continue to monitor and adjust protocols to meet the needs of the pandemic and of our people.
What have you learned about your team and its resilience during the pandemic?
For a company that is an essential business and has to keep the plant operating, our Essity team has demonstrated amazing flexibility. For example, there were times when, due to a necessary quarantine resulting from family contact, some shifts were down a person or two. To keep the machines running, we had team members jump in to cover a shift. We saw the regular 9-to-5 responsibilities of office staff (particularly human resources, safety and our plant nurse) shift to a 24/7 requirement. But everyone took it all in stride and worked their way through a health, safety and operational experience like no other.
What role has technology and innovation played in your COVID response?
Keeping 470 employees safe on site during a pandemic is no small undertaking, and we are regularly in touch with our counterparts at Essity’s other North American manufacturing sites as well as our global colleagues to learn about new technologies and best practices that can help us day to day. One of the most important innovations we implemented in the last few months is an upgrade to our air treatment – we installed ionization units to all 60 of our HVAC systems at the plant to increase air cleanliness. We also installed a walk-in temperature screener that provides instant readouts – something everyone on our staff appreciates. There is also new technology that indicates if/when you are closer than six feet from someone, which has been helpful when teams collaborate, as a reminder to maintain social distancing.
Aside from managing through COVID-19, can you tell us what else is happening at Essity, both internally, and out in the Shoals community?
There’s a lot going on! Here are some highlights:
- AmeriStar Awards: Every year, Essity hosts internal AmeriStar Awards, where employees are recognized for making the extra effort in areas like community involvement, safety, sustainability, cost savings, and project delivery. I’m proud to say that this year, three of our teams from Barton were nominated for this prestigious internal award, and we should hear results soon.
- FAME Girls’ Ranch in Russellville: We have a terrific partnership with the FAME Girls’ Ranch in Russellville. Prior to COVID, Essity’s Women of Steel group hosted over a dozen young women from the FAME Girls’ Ranch —one of four Alabama Sheriffs Boys’ and Girls’ Ranches in the state—to talk to them about their career aspirations and educate them about career opportunities for women in manufacturing. Once things are back up and running, we hope to host them again.
- Thanksgiving Meals Donation: In November 2020, Essity donated more than 1,000 Thanksgiving meals to the Salvation Army of Huntsville. With food insecurity on the rise in our community, we were glad we could help in this way.
- Community Involvement: In addition to our Shoals Chamber membership, every year we support our local high schools, food banks and schools through donations and in-person volunteer efforts.
- Fun fact: We opened our doors in 2003. Among our 500 employees, 135 have been here since day one! We also have 25 family members working here – a testament to the family environment and the great benefits of working at Essity.
Tell us about Essity’s commitment to sustainability.
Our Barton operations are part of Essity’s global network of manufacturing operations, and we are proud of the company’s commitment to sustainability—globally, locally and nationally.
In Barton, we buy in excess of 200 thousand tons of recycled paper per year, of which 65 percent goes out as finished product. The residual material also gets transformed into an alternative nutrient supplement for local farmland. From beginning to end, we are able to utilize almost all of the recycled material we take in. Just last week, in fact, Essity was ranked among the world’s top 100 most sustainable companies by Corporate Knights, which is an organization that compares global companies based on 24 indicators. We were also recently awarded the Platinum Medal in the 2020 Ecovadis CSR Rating. We have also been included in the Dow Jones Sustainability Europe Index in the Household Products Category. Everywhere Essity is, you are sure to find a sound foundation in sustainability.
Essity’s Barton facility expands well beyond its colloquial title as the Shoals-area “tissue plant.” With its devotion to the Shoals community, its employee recognition program, and its commitment to reducing its carbon footprint, Essity is more than just a business. It’s a model for business done right.